Miller Bros. Construction Reports: 2020 Progress and Completions
Mass-isolation foundations installed at Tredegar
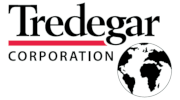
The Tredegar Flexible Packaging Films division produces specialized polyester (PET) films for use in food and industrial packaging applications.
Recently, Tredegar called upon MBCI to engineer and install mass-isolation foundations for two lathe machines in its plant in Pottsville, Pa.
Vibration isolation is required in order to avert precision lathe equipment from undergoing any unwanted vibration that could be transmitted from the surrounding building environment to the foundations that in turn will support the lathes.
Proper isolation between the machine foundation and its surrounding area invariably results in trouble-free machine operation.

- vibration study
- engineering of machine foundations
- saw cutting and excavation inside the building
- installation of sand base and isolation panels
- installation of reinforcing bar and concrete
Pipe Bridge project completed for AMCOR

The installation of an MBCI-engineered pipe bridge spanning a railroad siding for AMCOR in Allentown concluded in late December.

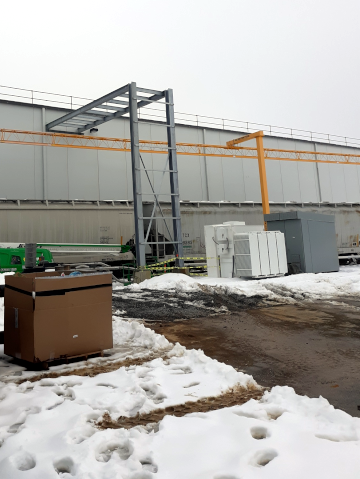
An electrical contractor is presently at the site installing conduit runs on our completed steel structure. The new conduits will supply much-needed additional power to this plastics manufacturing plant.
Yuengling Breaks Ground On Tampa Campus Expansion
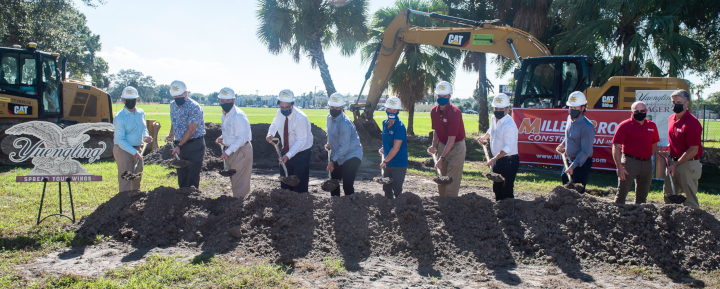
D.G. Yuengling & Son, Inc., America's Oldest Brewery®, broke ground on November 16, 2020 on a revitalization of its Yuengling Tampa Campus. MBCI is the general contractor for the development.
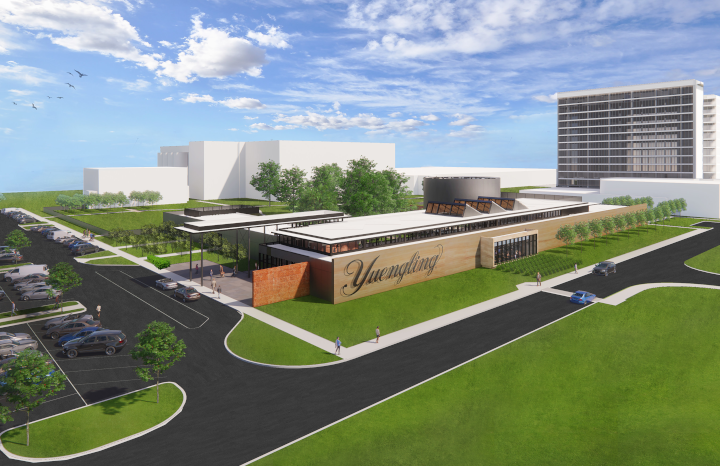
The Yuengling project includes a 15-story hotel, a restaurant, concert pavilion, gift shop, outdoor beer garden and private dining and conference rooms. The overall character of the design reflects Yuengling's rich industrial history as America's Oldest Brewery.
The new campus is slated to open in early 2022.
Specialty work for Amcor in Allentown
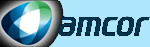
With 47,000 employees in more than 40 countries, Amcor is a global leader in developing and producing packaging for food, beverage, pharmaceutical, medical, home- and personal-care, and other products.
The Amcor Rigid Plastics USA plant in Allentown, Pa. required a new electric substation to sustain production capacity growth. MBCI was tasked with constructing concrete foundations and piers to support a design-build steel pipe bridge to carry electrical conduit over a railroad siding serving the facility.
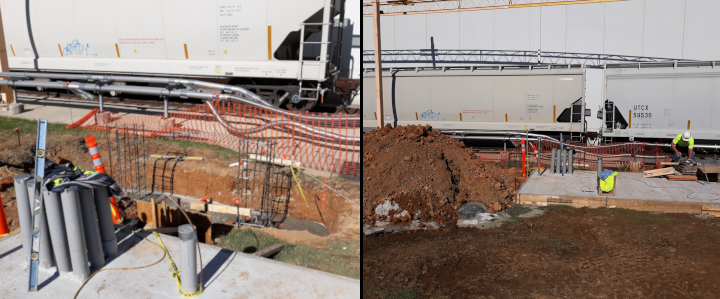
In addition, MBCI engineers submitted drawings for approval then fabricated in-house all the required steel. Placing the steel will require close coordination among Universal Electric – the contractor installing the substation, the Amcor maintenance team, and the railroad.
Work concludes on Miners Lofts Senior Housing Project
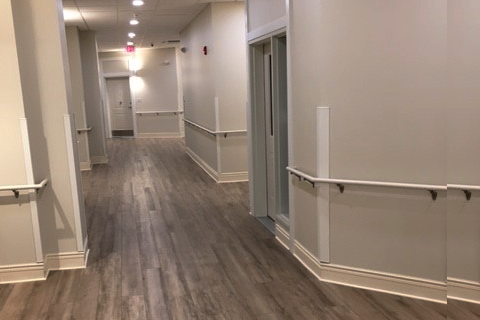
MBCI started work on the five-story Miners Lofts Project in November 2019.
The long-vacant former garment factory, comprising 64,375 square feet, is about to become the new home to senior citizens taking occupancy in 30 individual apartments.
MBCI’s scope of work comprised installation of metal studs, drywall, acoustical ceilings, door frames, doors and hardware, casework and countertops, wood trim, and toilet accessories.

In addition, we put down a concrete overlay on the second floor and poured new concrete on the ground floor. Work concluded in November 2020.
Rehab work at American Hose Company in Pottsville
MBCI was hired by the American Hose fire company to do various repairs on the exterior of the structure.
We installed new EIFS on several sides of the building. EIFS is a multi-layered exterior finish system. An abbreviation for "Exterior Insulation and Finish Systems," the material is also known as synthetic stucco.
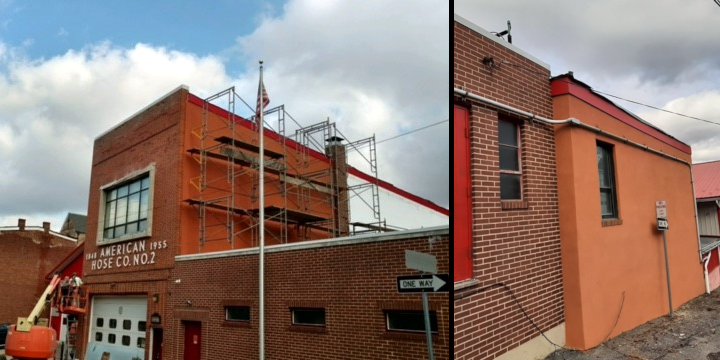
We repointed brick and replaced missing or damaged bricks. Installed a concrete walk at the fire escape area. Re-secured the fire escape to the wall and reattached broken fire escape railings, installed new fire escape support posts and repainted the fire escape.
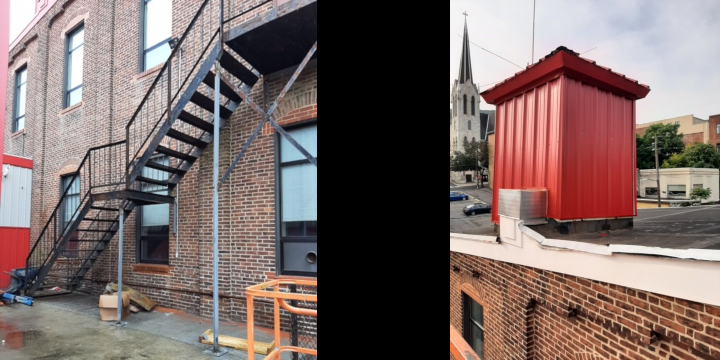
We completed the project in November 2020 upon the installation of new metal walls and roof panels on an existing cupola.
Rehab work at Penn State Student Commons Building in Wilkes-Barre
In September 2020 the Pennsylvaina State University contracted MBCI to rehabilitate a failing window wall in the Student Commons Building on the Wilkes-Barre Campus.

We removed two old, leaking aluminum storefront windows along with water-damaged studs and drywall.
Removed and replaced the associated roof structure.

Installed two new store front windows, new flashing and weather proofing as well as new exterior vinyl siding to make the entire system water- and weather-tight. We completed the work with new interior stud framing and drywall.
Students' living space is now protected from the vagaries of Mother Nature.
West Side Wood Products expansion project completed
West Side Wood Products specializes in custom wood packaging, such as skids, pallets, crates, and boxes in all shapes and sizes to suit customers’ specific shipping needs.
In September 2019 West Side Wood hired MBCI to add more production and office spaces to accommodate the firm's business growth. (see inset photo)

The scope of work included site preparation and erection of a 320’ x 200’ clear span structure to house increased production space and two-story offices. In addition, a detached 7,000 square foot garage was installed on the property.
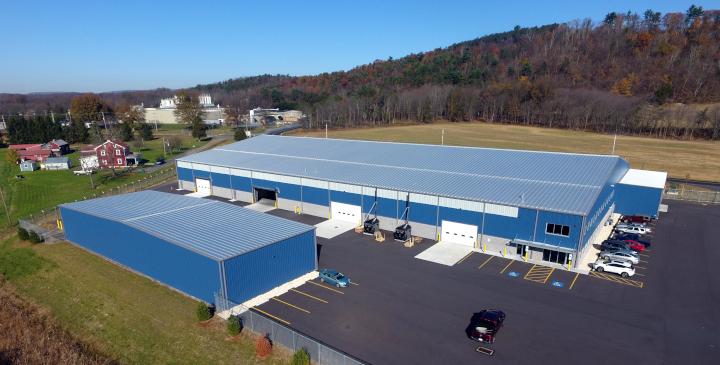

The project was completed in Summer 2020.
Interior makeover begins at the Robert E. Roeder Army Reserve Center
A total interior makeover of the Robert E. Roeder U.S. Army Reserve Center in Schuylkill Haven began in May.
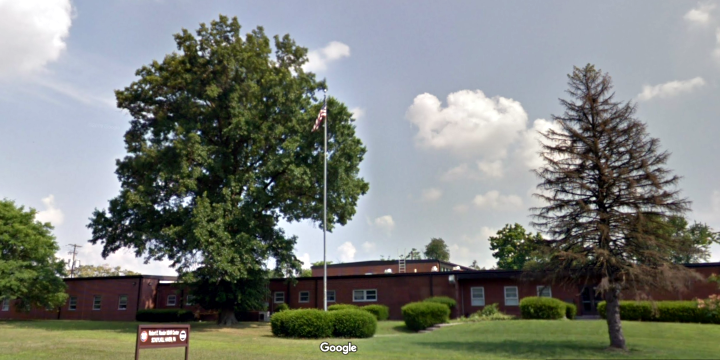
The scope of work includes new ceilings, wall paint, carpeting, vinyl composition tile flooring, markerboards and tack boards, even furniture.


Upgrades to electrical, data, and security systems are also part of the schedule.
The work is a design-build bid project for the U.S. Army Engineering and Support Center under the aegis of the Reliance Construction Company of North Carolina. Completion is expected in January 2021.
Groundbreaking ceremony for transit maintenance facility
On Tuesday, August 11, 2020, the Schuylkill County Transportation Authority (SCTA) held a groundbreaking ceremony to celebrate the onset of construction for a new Schuylkill Transportation System (STS) operations and maintenance center. Federal, state, and local officials participated in the event.
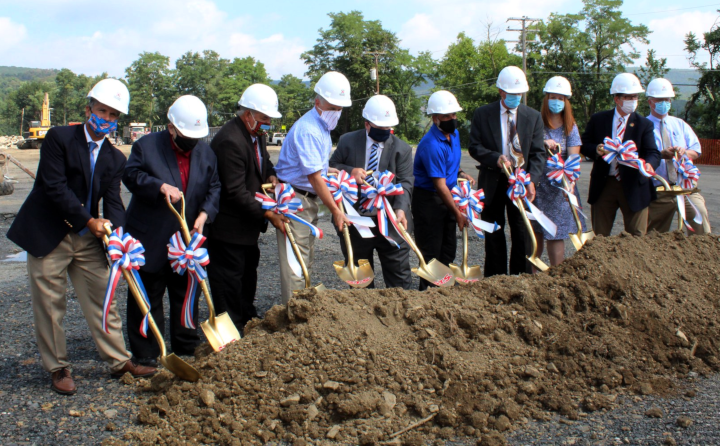
The 17-acre building site, located at 300 Wade Road in St. Clair, parallels the southbound lanes of Pa. Route 61.
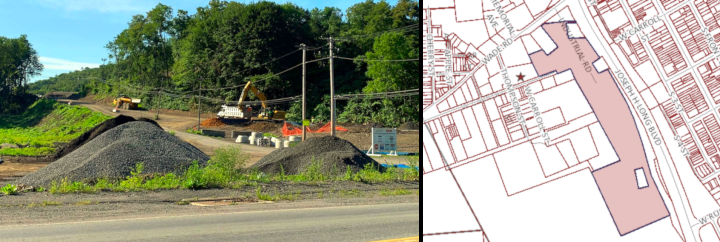
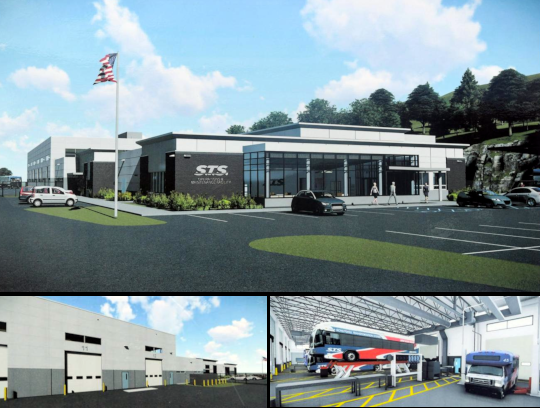
The planned 80,000 sf building is designed to house indoor storage, maintenance bays, administration space and a compressed natural gas (CNG) fueling facility for STS, a public transportation organization.
MBCI bid the project at $19.6 million on April 21.
SCTA issued a notice to proceed on May 18. Site work started on May 26.

Construction is expected to be completed by July 31, 2022.
NorthPoint Development welcomes MBCI for projects in Carlisle
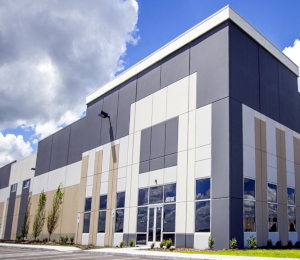
NorthPoint Development is a nationwide real estate firm specializing in Class A industrial properties.
One of the company’s newest Pennsylvania projects is a 380,069 sf industrial building at 1700 Harrisburg Pike in Carlisle, Pa.
MBCI was invited to complete office space fit outs for two separate tenants in the same building. Both projects have very aggressive production schedules.
Project 1 This project comprises preparation of a 40-foot high space of 310 feet in length demising to separate sub-tenants and space for an office consisting of 2,960 sf. Project start date June 23 with expected turnover on or before August 31, 2020.
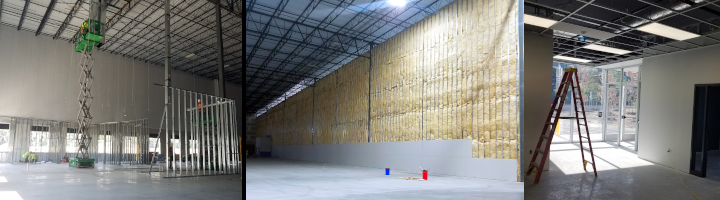
Project 2 This project includes 8,150 sf in total: office space of 2,350 sf and showroom space of 5,800 sf. Project start date on July 1 with completion of offices scheduled for August 31 and turnover of the showroom on or before October 1, 2020. The scope of work also includes cutting in new openings and creating nine dock positions.
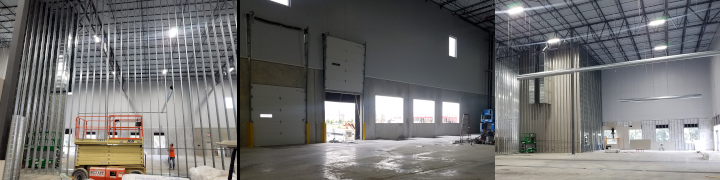
MBCI tackles major spiral freezer installation for Michael Foods

Michael Foods Inc. processes and distributes refrigerated and frozen egg products to restaurants, retail, grocery, and convenience stores around the globe.
MBCI possesses a years-long history of successfully completed construction projects for the managers of the Michael Foods Inc. processing plant in Klingerstown Pa. When two spiral freezers began showing their age and needed replacement, Michael Foods hired MBCI to perform the architectural and structural segments of the project.
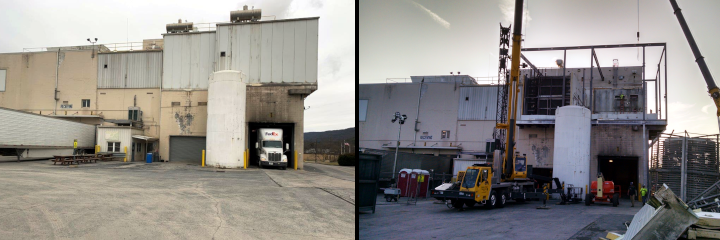

Spiral freezers serve as lifelines to many food production processes. No spirals mean no production.
These freezers were huge. So big they took up two floors. One measured 28 x 38 x 21 feet high; the other was 21 x 34 x 21 feet high. Both commanded spaces on the third and fourth floors of the facility and included elaborate drain systems for collecting leaking water.
MBCI took the lead on the project, delivering services covering the entire spectrum: designing, drafting, engineering, permitting and construction.
Since replacement time was of the essence, a 76-day production schedule was established.
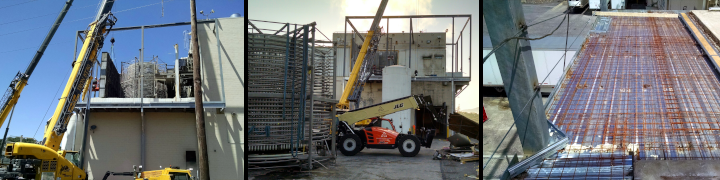
The old freezers were integral to the structure since the north and west walls of the freezer space were exterior walls of the building. The work started more than 30 feet above finish floor (AAF) and topped out at 62 feet. We had to extend the building outward three to nine feet around the north and west walls and upward six feet to accommodate the new stainless-steel equipment.

The replacement freezers required protection from the elements during construction. They could not be exposed to sunlight or rain. We erected a 30 x 50 x 24-foot pole building in the parking lot for protection of the spirals.

The third and fourth floor spaces where spirals were to be installed had to be kept enclosed even while still allowing the spirals to be dropped in by crane from overhead. We needed to be inventive.
We conceived and created a 2,500-sf retractable tarp roof using cables, pulleys, ropes and two exceptionally large tarps.
Some snickered when they heard the idea. But it worked.

The sides would also be a challenge, requiring installation of gigantic tarps to enclose them. All this while protecting the floors below from any water damage.
The lower floors contained training rooms, offices, and breakrooms. We performed our work with little disruption to staff and no damage below. However, we did remove and replace ceilings in the occupied area where old leaks from the original spirals had occurred.
We worked double shifts and frequently weekends to maintain the production schedule. Some weeks went by with no days off to maintain the pace.
Most of the work was carried out at more than 30 feet AFF. In such an environment, safety is always our #1 priority. We installed steel curbs, railings, cables, and D-hooks everywhere as needed during this project to maximize worker safety.
Project started in June and completed in early August.
While this project was continuing and plant production was slowed, Michael Foods asked for additional drain work to be done concurrently. In carrying out the request, we demolished hundreds of feet of trench drain on the production side of the elevated third floor slab and installed nine new spot drains.
Floors were re-sloped and epoxy coated. We installed temporary walls during this work so the remaining building would be unaffected and production could continue in those areas.
MBCI completes new office fitout for NorthPoint Development
In the final quarter of 2017, NorthPoint Development acquired a 248,640 sf industrial building at 32 Earth Conservancy Drive in Wilkes Barre, Pa. It was purpose built for warehouse and distribution functions.
This year, in preparation for a new tenant, NorthPoint hired MBCI to complete a series of interior improvement projects.
Our scope of work included new offices, conference room, rest room, truckers vestibule, and shipping office in approximately 2,000 square feet of interior space.
New work comprised flooring, paint, ceilings, doors, breakroom casework, light fixtures and transaction areas. In addition we installed three new dock openings and dock equipment, and three new battery charging stations with roof mounted exhaust.

Contract awarded end of May. Project completed August 1.
MBCI completes new HQ for Danville police department
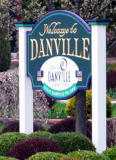
In June 2020 MBCI completed construction of a 10,130 square foot building that will serve as the new headquarters of the Danville, Pa. Police Department.
The exterior facade mirrors that of many newly-constructed state police barracks buildings. Windows are small by design and placed high in the wall to be consistent with present day security practices.

The interior of the steel and masonry structure includes interview rooms, evidence storage room, chief's office, patrol office, conference room, fitness room, and lockers and shower.

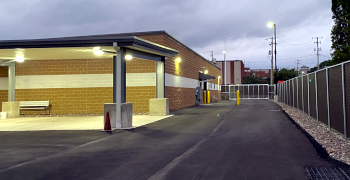
Of particular interest to the members of the department is the enhanced security provided by a feature known as a sally port. The dictionary defines a sally port as a "secure, controlled entry way to a fortification or prison." Vehicles transporting people under arrest remain inside the building until detainees are securely removed from them or positioned inside them.
MBCI begins 2020 with new projects for NorthPoint Development
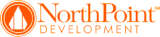
NorthPoint Development is a privately-held, national real estate development firm specializing in the development of Class A real estate facilities.
MBCI has built a history with the firm of successfully delivered projects.

NorthPoint once again called on MBCI to complete two tenant improvement projects within existing commercial-industrial buildings. One located in Hanover Township and the other in Wilkes-Barre Pa. NorthPoint wanted the two projects to track concurrently according to a tight schedule, with completion for both no later than the end of February 2020.
Project supervisors for NorthPoint tenant Johnson Health Tech – a Taiwan-based fitness equipment company enjoying a global reach – witnessed the MBCI team carve out 3,722 sf of space from within the huge Tradeport 164 Building 1, located in Hanover Township, Pa. In addition to offices the team created a breakroom, restrooms with showers, satellite restrooms and a patio area. Project start date: December 30, 2019. Completion: February 28, 2020.
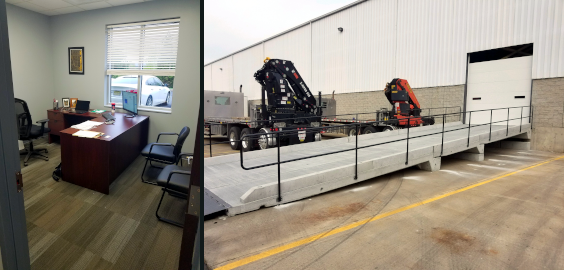
The second project comprised a not-dissimilar bundle of objectives for NorthPoint tenant National Cart Company within a building located at 32 Earth Conservancy Drive in Wilkes-Barre.
National Cart, headquartered in St. Charles, Missouri, is a family-owned and operated business and a leader in design, manufacturing, and distribution of material handling products, food service products, and store fixtures.The scope of work included a total renovation of 1,500 sf of office space with all new HVAC, electrical, flooring, ceilings and paint. MBCI specialists also carried out warehouse renovations that included installation of new dock equipment for existing doors, creation of a new wall opening for a drive-in door and an access ramp. Project start date: February 1, 2020. Completion: February 28, 2020.
MBCI completes its fifth VA Clinic for STGi
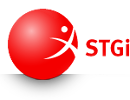
STG International, Inc. (STGi) contracts with Federal government entities like the Veterans Administration to design, build, staff and manage healthcare clinics that deliver primary care, mental/behavior health, women’s health, radiology, telehealth and other services.
STGi awarded MBCI the contract for interior fit out of a new VA clinic in a 10,000 sf former school building in Plattsburgh, New York. This was MBCI’s fifth VA clinic project undertaken for STGi.
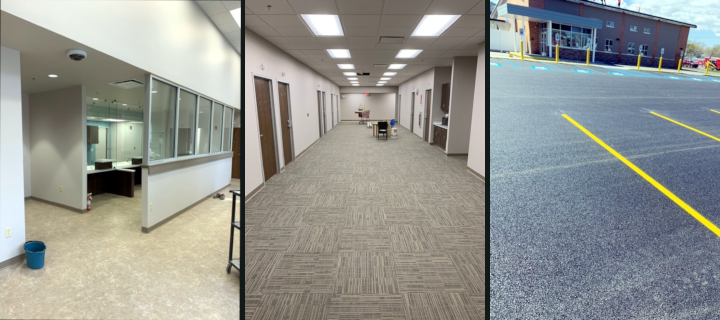
The existing interior was gutted to allow the creation of new interior spaces. Exam rooms, rest rooms, break area, utility spaces, waiting area and new entry vestibule were created. A new, durable, synthetic rubber roof (known as EDPM roofing) and facia was installed. The parking lot was re-paved along with new line striping.
The originally anticipated completion date was March 31. As a result of the shutdown related to the Covid-19 pandemic, we ultimatelyfinished the project during the first week of May.
MBCI razes and replaces ramps for Big Lots Distribution Center
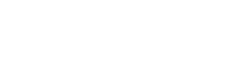
Headquartered in Columbus, Ohio, Big Lots, Inc. is a community retailer operating more than 1,400 Big Lots stores in 47 states.
The Big Lots Distribution Center in Tremont Pa. called on MBCI to replace two existing exterior forklift ramps.
Each concrete ramp measured approximately 70 feet in length and 16 feet in width.
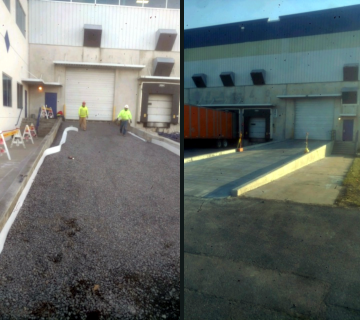
We razed the existing ramps and removed existing ramp wall guardrails.
We formed and poured new concrete ramp walls and 8-inch thick forklift ramps.
We finished the project with the installation of new metal guardrails.